Grain structure
Grain is a small region of a metal, having a given and continuous crystal lattice orientation. Each grain represents small single crystal.
Grains form as a result of solidification or other phase transformation processes. Grains shape and size change in course of thermal treatment processes (for example recrystallization annealing). The normal grain size varies between 1µm to 1000 µm.
Grain structure of a solid is an arrangement of differently oriented grains, surrounded by grain boundaries.
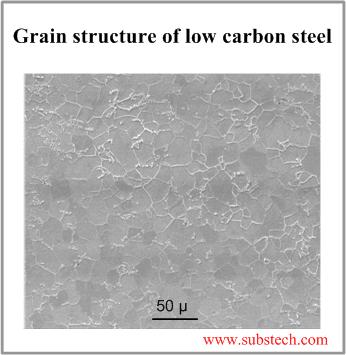
Formation of a boundary between two grains may be imagined as a result of rotation of crystal lattice of one of them about a specific axis.
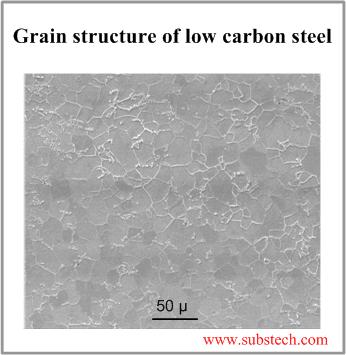
Formation of a boundary between two grains may be imagined as a result of rotation of crystal lattice of one of them about a specific axis.
Depending on the rotation axis direction, two ideal types of a grain boundary are possible:
- Tilt boundary – rotation axis is parallel to the boundary plane;
- Twist boundary - rotation axis is perpendicular to the boundary plane;
- An actual boundary is a “mixture” of these two ideal types.
Grain boundaries are called large-angle boundaries if misorientation of two neighboring grains exceeds 10º-15º.
Grain boundaries are called small-angle boundaries if misorientation of two neighboring grains is 5º or less.
Grains, divided by small-angle boundaries are also called subgrains.
Grain boundaries accumulate crystal lattice defects (vacancies, dislocations) and other imperfections, therefore they effect on the metallurgical processes, occurring in alloys and their properties.
Since the mechanism of metal deformation is a motion of crystal dislocations through the lattice, grain boundaries, enriched with dislocations, play an important role in the deformation process.
Diffusion along grain boundaries is much faster, than throughout the grains.
Segregation of impurities in form of precipitating phases in the boundary regions causes a form of corrosion, associated with chemical attack of grain boundaries. This corrosion is called Intergranular corrosion.